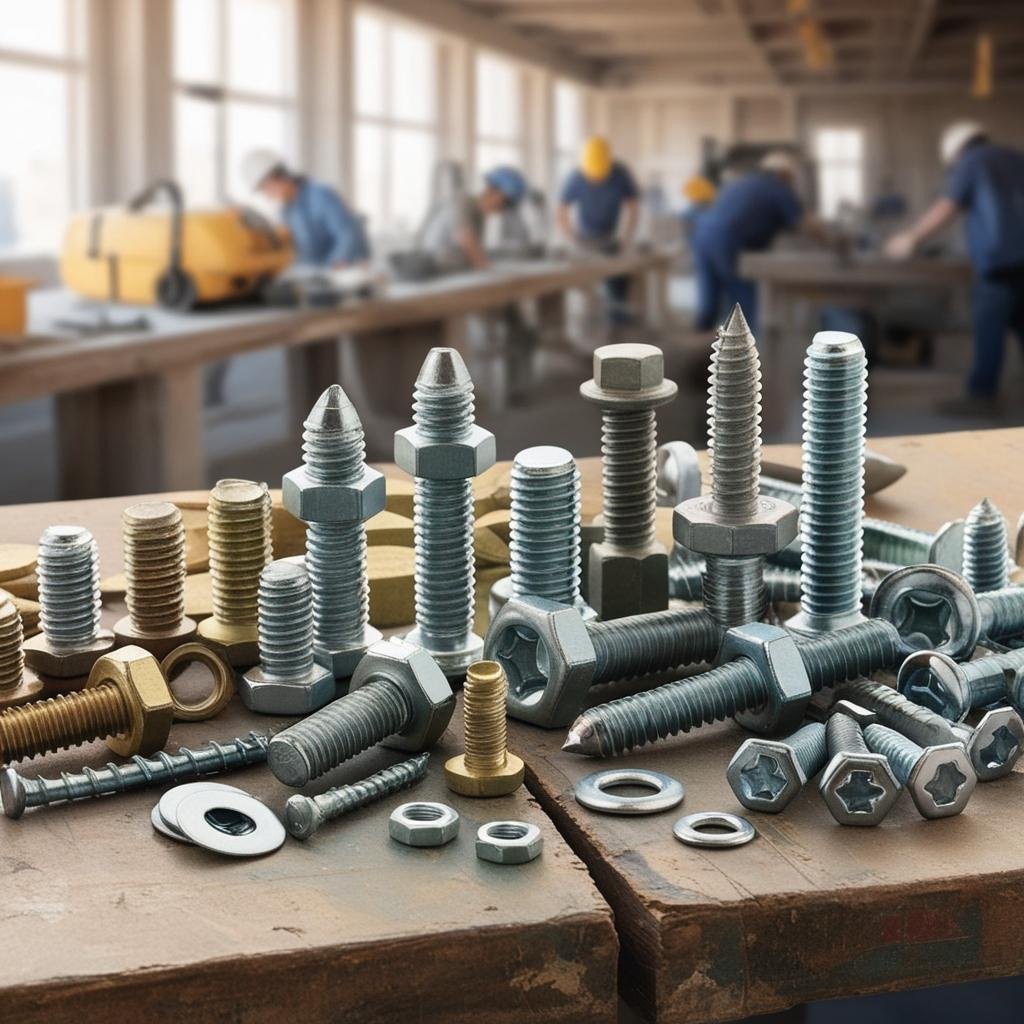
Observation is the key to find the problem
It is a big setup with many stages in the production line. From receiving raw materials to passing through various development stages and finally storing finished materials in the warehouse for later dispatch to clients, with quality checks at various stages - it looks like a complex process when someone sees the setup of this company for the first time, especially those new to the fastener industry, but not for those who work in it. This company is one of the third-party vendors for another big company. This other company is one of India’s leading manufacturers, assembling motors, generators, pumps, lathe machines, and many more products for industrial use. The process described above is of the vendor company who is one of the suppliers to this big company. This small manufacturing vendor company was facing two major problems:
Constant complaints of quality issues from the big company with respect to raw materials used. The vendor company wanted to supply the finished materials in FIFO (First In, First Out) order, which was not happening.
There were other issues as well, but they are not within the scope of this article, hence keeping them out. The in-charge of the company unit, for which there were constant complaints, took the initiative and got permission from the company head to appoint a consultant in order to review the process, find issues, propose solutions, and implement them as a pilot for the given company unit. The consultant was appointed, and the consultant team went through the process and phases of development. After analysis, the consultants submitted a report, of which the following are the summarized points for the stated two major issues:
- Raw materials used to prepare finished goods for the client company were not of the standard specified by the client company. However, the vendor company purchases the materials at extra cost as per quality standards specified by the client company. The problem is - these materials get mixed up with other purchased raw materials. When the time comes to pick the raw materials, it all depends on the employee to pick the right materials. There is no guaranteed way to ensure the right materials are selected.
- There is an open area with virtual boundaries where materials are stocked. Rules have been defined for employees on how to store and pick the materials, but these are not being followed as there is no system to ensure that materials are stored and picked in the correct order.
It may look trivial to solve these problems, but identifying them was not easy unless you observe how materials are being picked and stored over a long period. There were proper signs in the local language, and a store in-charge was present when these transactions were happening (specifically when consultants were observing, staff were extra cautious to pick and store the materials correctly).
Observation was the first key to look at the operations and figure out the problem. Late consultant team suggested to solve above two major problem with the following approach:
- Physical Segregation and Color Coding, Material Tracking System, Quality Verification Process
- Physical Storage Redesign, Visual Management System, Process Controls, Training and Incentives
To know more about details for each of the steps, feel free to reach me here.